Acoustic Blankets Reduce Chiller Noise
Just as thermal insulation keeps in heat, acoustic insulation blankets keep in sound. Just covering a compressor isn’t enough to reduce chiller noise unless an insulation maker also pays attention to equipment geometry. The State University of New York at Oneonta learned about the benefits of covering compressors thanks to Shannon Global Energy Solutions.
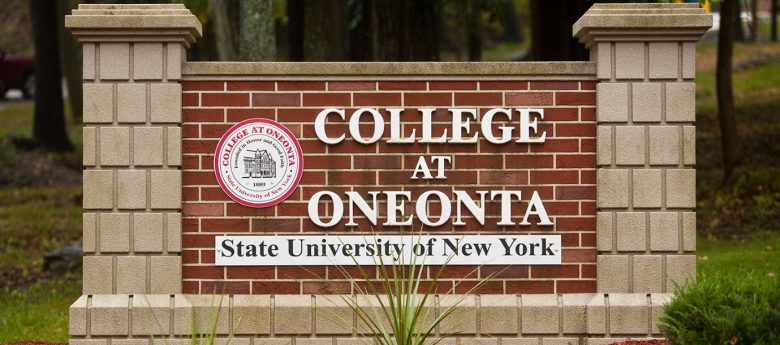
Just as thermal insulation keeps in heat, acoustic insulation blankets keep in sound. Just covering a compressor isn’t enough to reduce chiller noise, though, unless an insulation maker also pays attention to equipment geometry. That means ensuring there are no gaps between the reusable insulation and the component covered. Any gap helps sound energy escape the blanket. So, if you’ve covered your components or equipment with acoustic blankets and still hear noise, then it may be the result of a few (possibly several) gaps between the insulation blankets.
The State University of New York at Oneonta learned about the benefits of covering two compressors on a Trane Model RTAA Rotary Liquid Chiller; the removable-reusable acoustic insulation reduced the noise level affecting classes at its Human Ecology Building.
Before covering the compressors with a set of Shannon LT250A-VP reusable acoustic blankets (which Shannon Global Energy Solutions designs specifically for HVAC equipment such as liquid chillers) instructors were distracted by the operation of the chiller’s compressors and fans. Although elastomeric vibration eliminators can reduce structurally transmitted sound, the chiller’s uninsulated compressors disturbed instructors and students in class.
Shannon and its reseller Altamont, N.Y.-based Technology Plus learned about the acoustic challenge with the chiller located near the Human Ecology Building while helping the college’s facilities team evaluate the use of reusable thermal insulation blankets for a set of valves located in the campus’ tunnels.
“The SUNY team felt there wasn’t much they could do about the chiller noise,” said Terry Roach, major account manager for Shannon. “We looked at the situation and system; the compressors have some unique geometries, but we always find a way to accommodate that.”
“We recommended the LT250A acoustic blanket,” said Paul Megan, Inside Sales manager for Technology Plus. “Covering a compressor isn’t enough to reduce chiller noise; you also have to carefully design the reusable insulation, so when a maintenance worker takes it off and puts it back on the component there are no gaps, which cause sound energy to escape. You don’t want maintenance staff struggling to get the blanket to fit – it should be easy, which is where good design and standards come in.”
“The blankets perform well; once Shannon made them and shipped them to us, we installed them ourselves, and they go on and come off easily,” said Terry Zimmer, director of Facilities Operations for SUNY Oneonta. “The sound is noticeably different, since putting the acoustic blankets on.”
According to Shannon, there has been a reduction in noise of 6 dBA since blanketing the SUNY Oneonta compressors.
When considering acoustic insulation, a facility manager should work with an insulation manufacturer who’s trained to carefully measure and inspect a noisy component or machine. An experienced insulation maker can make recommendations, if needed, for decoupling the noise-making machine from the ground with a vibration isolation device like a shock absorber, spring, or wire rope isolator. Making the insulating process highly successful requires reducing the transfer of sound pressure to other locations within or across a machine. For instance, residents and officer workers in surrounding buildings can hear a roof top chiller, especially if situated on a taller building.
If your aim is to reduce chiller noise or the sound emanating from any other type of component, take these steps today:
- Download a free decibel meter app like the NIOSH Sound Level Meter. Determine a measure for what you’re hearing and compare that to OSHA permissible noise exposures.
- Next, inspect the machine you’re going to insulate. Does it appear to be decoupled and isolated from its surroundings, or is its simply bolted to a roof, concrete pad or wall?
- Third, contact an acoustic insulation blanket maker who designs products in accord with ANSI/AHRI Standard 575.
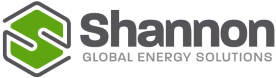