Caterpillar Delivers Power for Research
In a state-of-the-art building on the southern end of the Auburn University campus, more than 325 Edward Via College of Osteopathic Medicine first-and second-year students are taught the fundamentals of osteopathic medicine. Continuous, uninterrupted power is a critical element that supports virtually everything that takes place within the walls of the four-story, 100,000-square-foot building.
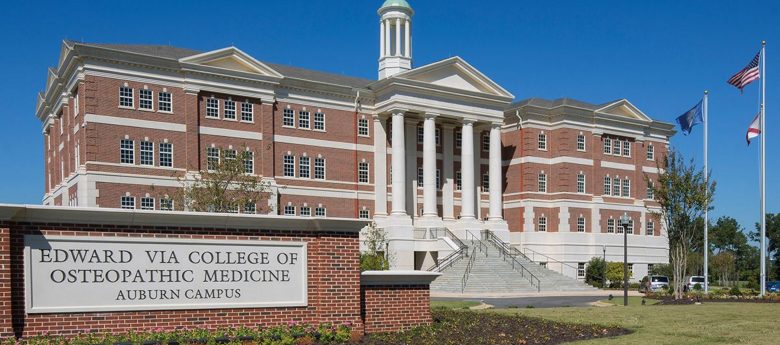
In 2011, the former president of Auburn University visited each Alabama county and saw the extreme need for rural physicians that provide primary care. Officials at Auburn University (AU) recognized abysmal health outcomes in Alabama and the extreme shortage of physicians – then ranking 46th in the country for number of physicians per 100,000 population.
The situation in Alabama mirrors a national trend. A study in 2002 reported in Health Affairs estimated a shortage of 50,000 physicians in 2010 and more than 100,000 physicians by 2020.
The conclusion reached by former Auburn president Dr. Jay Gogue and AU administration was that establishing an osteopathic medical college would best fill this need.
In the meantime, a model for establishing a non-profit medical school to address the shortage of rural physicians was already well established on the campus of Virginia Tech. The Edward Via College of Osteopathic Medicine (VCOM) opened its doors in the Virginia Tech Corporate Research Center to the first students in fall 2003 and graduated its first class in 2007.
VCOM’s founding vision was to provide healthcare for the underserved regions of Southwest Virginia, Western North Carolina, and the Appalachian Region, and to promote biomedical research with Virginia Tech.
In response to the enrollment of a significant number of students from western North Carolina and South Carolina, VCOM opened a second Carolinas campus in Spartanburg, South Carolina in 2011. Recognizing the success of VCOM and Virginia Tech collaboration, AU representatives visited both the VCOM Virginia and Carolinas campuses prior to opening VCOM-Auburn as a fully accredited branch campus in 2015.
In a state-of-the-art building on the southern end of the Auburn University campus, more than 325 VCOM first-and second-year students are taught the fundamentals of osteopathic medicine – which incorporates basic science, anatomy, physiology and biochemistry. During their third and fourth years, the medical students are assigned to clinical rotations at hospital sites that serve rural areas.
“We have a history of recruiting students from rural areas,” says Dr. Elizabeth Palmarozzi, dean of VCOM-Auburn. “We try to educate them not only here on campus, but we arrange for them to work in rural areas for their clinical experiences, and that encourages them to want to go back to a rural area when they graduate.”
The approach works, as approximately 67 percent of graduates go on to practice in underserved areas.
“When I first interviewed back in 2003, VCOM-Virginia hadn’t been built,” adds Dr. Jeremy White, an associate dean at VCOM- Auburn who was part of the school’s first graduating class in 2007. “I took a chance on a school that hadn’t even been built yet, and 15 years later, I can attest to the founding promise that we offer a unique experience in medical education.”
Continuous, uninterrupted power is a critical element that supports virtually everything that takes place within the walls of the four-story, 100,000-square-foot building.
VCOM’s curriculum is based on a digital platform. Lectures are given on PowerPoint presentations and recorded so students can access them if they’ve missed class or need to refer back. Exams are also administered digitally.
“These students have so much information thrown at them over four years that anytime they can retrieve the data that they need, the faster and better for them when they’re cramming and studying,” says Shayfer Mosness, director of information technology at VCOM-Auburn.
“Keeping the power on is also critical for the HVAC systems, because my audio-visual and data rooms need to stay cool,” Mosness adds. “Here in Auburn, Alabama, it gets hot quickly, so we need to keep those HVAC units running.”
A Simulation Center provides state-of-the-art technology for students to practice while honing their diagnostic skills. The VCOM-Auburn building also features a large osteopathic manipulative medicine lab with electrically adjustable tables, and a first-class anatomy lab.
Maintaining the anatomy lab at the proper temperature and humidity levels is essential for preserving the cadavers so the students can practice on them, says Randy Cerovsky, facilities director for VCOM-Auburn.
Aside from HVAC requirements, the Simulation Center is the most power-intensive department in the building. Activities include standardized patient encounters where students interact with patient actors (the mock clinical sessions are recorded), then return during their rotations and have simulated patient encounters.
Procedural skills training involves tasks such as IV placement, tracheal intubations, and suturing. High-fidelity mannequins simulate various patient presentations and critical patient encounters.
“We need uninterrupted power, especially because we are very testing intensive,” White says. “We are evaluating 160 students at a time in a meticulous environment, and if there is any disruption in our testing environment, it can invalidate our testing scenario and compromise what we’re trying to achieve here. So uninterrupted power is critical to what we’re doing for all three of our offerings in the simulation department.”
Solution
To ensure the power is always on, VCOM installed a Cat G3412 gas generator to back up the utility feed at the Auburn campus when the building first opened.
The consulting engineer on the project recommended a gas generator because gas service was already available for some labs in the building.
“The theory was to avoid any disruptions from service trucks having to come here and fill diesel tanks with fuel, as well as potential problems maintaining the quality of the diesel fuel,” Cerovsky says.
Results
Outside of several brief outages, the Cat generator set has seen extended run time once for an outage of about five hours when AU cut off power during construction of a nearby nursing school. Every Friday, the generator automatically runs for 15 minutes to ensure the system is in proper working order. Based on a recommendation from Cat dealer Thompson Tractor, VCOM transfers the electrical load to the facility once a month.
“Every time, the generator has kicked right in and done what it’s supposed to do,” Cerovsky says. “We have never noticed any delay in the amount of time it takes for the generator to start up and transfer the power over. Everything just runs smoothly. We’ve never had any issues.”
Cerovsky and Mosness receive email alerts whenever the generator set runs, and also notifications if any issues arise. This is helpful when the generator starts and runs for something other than a routine test, Cerovsky says.
“One of the features I like best about our Cat generator is the Cat Connect interface that enables us to receive SMTP notifications,” Mosness says. “So, if there’s anything wrong with our generator—whether it’s starting, running, stop, default, or low fluids—we get notifications and then we can reach out to our sales rep and receive service immediately.”
Technicians from Thompson Power Systems perform regular maintenance on the generator set.
“Thompson Power Systems has been great to work with,” Cerovsky says. “When we call them, if they can’t get here that day, we get a prompt response the next day. They do all of the service, and they explain everything. Not using the system every day, we sometimes forget some operating details that you need to know about.
“And Thompson is always very helpful and willing to do whatever it takes.”
For more information, please visit www.catgaspower.com.
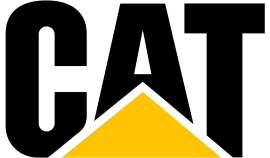