Cooling Emergency Turns into No-Cost Upgrade
For a rural county school district in Kentucky, it started with an emergency failure of a cooling tower used with the school’s HVAC system. The old tower had required significant maintenance over the years. However, the district was hoping to delay the expense of having to replace it along with another metal tower utilized by the high school that was also nearing end-of-life.
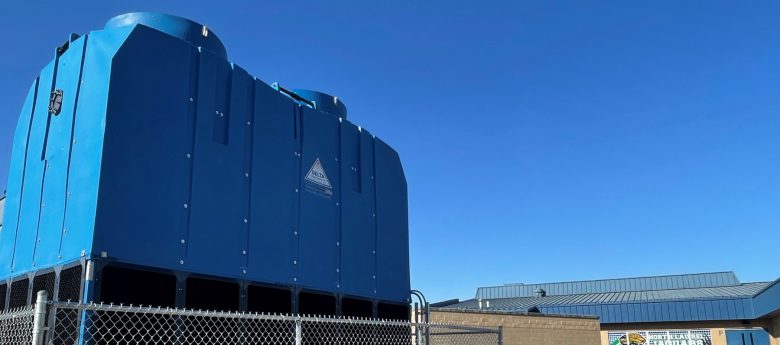
For a rural county school district in Kentucky, it started with an emergency failure of a cooling tower used in conjunction with the school’s HVAC system. The old, metal-clad cooling tower at the area middle school had required significant maintenance over the years. However, the district was hoping to delay the expense of having to replace it along with another metal tower utilized by the high school that was also nearing end-of-life.
“They needed a new tower, fast. Theirs was in real bad shape from years of rust buildup and they were experiencing all kinds of leaks – panel leaks, gasket leaks, everything,” explains Zach McKinney, sales engineer at Bluegrass Hydronics and Pump, which helped the school district with the cooling tower replacement.
Often in an emergency situation, researching for optimal replacement options gets tossed aside for what can be done quickly and easily. Fortunately, for the school district, the team at Bluegrass had experience with advanced engineered-plastic cooling towers. The units would end up solving the two biggest issues the school district was facing: budget and durability.
Going for the Grant
To cut costs, McKinney had a plan. He knew that some engineered plastic cooling towers are now being manufactured with antimicrobial properties. He believed this would qualify them for government funding under the Elementary and Secondary School Emergency Relief (ESSER) program.
Created by the CARES act, ESSER funds are awarded to schools in need of repairing or improving facilities – the caveat being those improvements must reduce exposure to environmental health hazards. Originally intended for COVID relief, the program was expanded in 2021 to include other environmental health and safety projects that do not have to be directly related to coronavirus.
Antimicrobial engineered-plastic cooling towers were first designed to help prevent the outbreak of the often-deadly Legionnaires’ Disease. Unlike metal towers, engineered plastic can be molded so that special antimicrobial additives are compounded throughout the plastic. These resins contain wide-spectrum additives that operate on a cellular level to continuously disrupt and prevent uncontrolled growth of microorganisms and biofilm within the cooling tower.
“It worked! The school district was awarded the grant and was able to acquire both towers at no out-of-pocket expense,” says McKinney.
A Textbook Case
The adoption of antimicrobial cooling towers has become increasingly important because of the growing number of outbreaks of Legionnaires’ Disease at numerous locations throughout North America. In fact, each year about 18,000 people are infected with the Legionella bacteria in the United States alone.
Legionnaires’ disease is a severe form of lung infection caused by exposure to bacteria known as Legionella. Found naturally in freshwater environments like lakes and streams, Legionella becomes a health hazard when it grows unabated in water that is not properly treated. While this can include showerheads, hot tubs and hot water heaters, a significant number of outbreaks have originated in cooling towers.
“A cooling tower is the perfect breeding ground for Legionella because it’s wet and humid and exposed to sunlight,” explains McKinney. “The Legionella will colonize the walls of the tower, and the colony will grow bigger and bigger.”
Cooling towers have a long history of effectively expelling heat from the water used in many commercial and industrial applications. However, even when they are disinfected and properly maintained cooling towers are potential breeding grounds for legionella, according to the Centers for Disease Control and Prevention (CDC).
Legionella bacteria spreads to humans when expelled water vapor or mist containing the bacteria is inhaled. For this rural Kentucky school district, the location of their cooling towers amplified their concerns over this issue.
“One of the towers sits right by the football stadium,” says McKinney. “Can you imagine if they had an outbreak right there with all those people in the stands? That would be bad news!”
Back to School on HDPE
The antimicrobial cooling towers that the school district ultimately selected were manufactured by Delta Cooling (www.deltacooling.com). The company pioneered engineered plastic cooling towers in the 1970s and recently innovated the first cooling towers that featured antimicrobial resins in not only the fill, but the entire base cooling tower structural material, sump, and drift eliminator.
The engineered plastic towers are made out of high-density polyethylene (HDPE), which is impervious to the natural and chemical causes of rust and corrosion. The towers are also unaffected by pH from water sources, including evaporation make-up water, and even the water treatment chemicals that attack metal towers from the inside out. This solved the second issue for the school district.
“Durability was a huge part of what won us that job,” adds McKinney. “With HDPE, the whole tower is molded in one piece, so you don’t have any of the leaking points that caused the failures in metal towers. Plus, it doesn’t hurt that Delta puts a 20-year warranty on their towers. You just don’t get that kind of lifespan with metal towers.”
To further reduce ongoing cost and maintenance requirements, the school district also wanted to get away from the belt-driven fan systems that require periodic downtime for replacement. The Delta Cooling direct-drive fan eliminates the belts entirely. In addition, the variable-frequency drive (VFD) motor, which requires less horsepower than their previous towers, is already translating into substantial savings on electric power consumption for the school district.
“We are actually already working to roll this out again at other schools,” concludes McKinney. “The ESSER funds are still available, and with these antimicrobial HDPE cooling towers, we know we can help other schools improve their situation.”
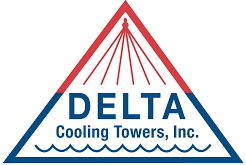