Insulfoam Rebuilds Hospital Roof
A Missouri hospital rebuilds stronger after a force five tornado largely destroyed most of the St. John’s Regional Medical Center in Joplin. By using Insulfoam 15” Tapered EPS as part of the roof system on the new hospital (now known as Mercy Hospital Joplin), the resulting structure is 30% stronger than the requirements for the old hospital.
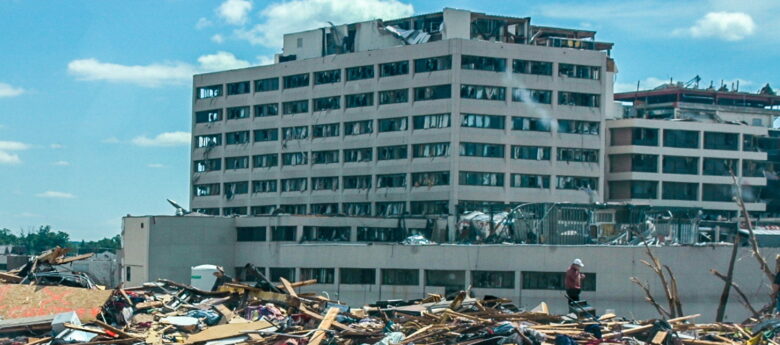
After a force five tornado destroyed St. John’s Regional Medical Center on May 22, 2011, the Joplin, Missouri hospital rebuilt with a new stronger facility designed to stand up to devastating wind forces. After the destruction, architects and engineers analyzed how the nine-story structure – especially its roof – reacted to the storm. Today, a new facility stands stronger with a big tornado in mind.
One of the largest changes to the hospital was the roof in an effort to harden the hospital’s building envelope. More than any other part of a building, its roof system components must complement each other. Insulation is a crucial component, because it contributes to a roof system’s thermal performance and overall durability while providing a substrate for the roof membrane. Tapered Insulfoam was used to help the new hospital roof combat strength, water absorption, stability, stable R-Value and excellent performance.
In the old facility, the design team learned that the metal with insulation on top was removed by the tornado and exposed the inside of the building. The roof is all concrete decks with a double roof system and a waterproof membrane. The result is that if the hospital loses the roof system, there will still be a watertight and concrete-sealed building.
Pre-cut tapered EPS blocks were used to increase roof slope for additional drainage, while offering a long term, stable R-Value, excellent dimensional stability, compressive strength and water resistant properties that meet or exceed the requirements of ASTM C578. The thick blocks can be factory-cut into single -layer tapered pieces that eliminate the labor of stacking multiple insulation panels. Tapered EPS can be adapted to accommodate any roof drainage system and roof configuration.
Insulfoam Tapered Insulation
Labor Savings: There are no complicated filler panels systems. Tapered InsulFoam can be installed in a single layer for thicknesses up to 40”, making it significantly more cost effective than comparable rigid-insulation tapered systems. The ultra-lightweight nature of Insulfoam EPS further allowed for fast installation.
Promoted Positive Drainage: Tapered InsulFoam is the ideal insulation for both new construction and re-roofing projects in which positive slope is desired or ponded water is a concern.
Environmentally Friendly: 100% recyclable if ever removed or replaced, Insulfoam EPS contains no formaldehyde or ozone-depleting HCFCs.
Stable R-Value: EPS’s thermal properties will remain stable over its entire service life. There is no thermal drift, so the product is also eligible for an Insulfoam 20-year thermal performance warranty.
Proven Performance: The same fundamental EPS chemistry has been in use since the mid-1950’s so the actual performance of the product is well known.
Water Resistance: Tapered Insulfoam does not readily absorb moisture from the environment.
Code Approvals: Tapered Insulfoam is recognized by the ICC-ES and has numerous Underwriters Laboratory and Factory Mutual approvals.
